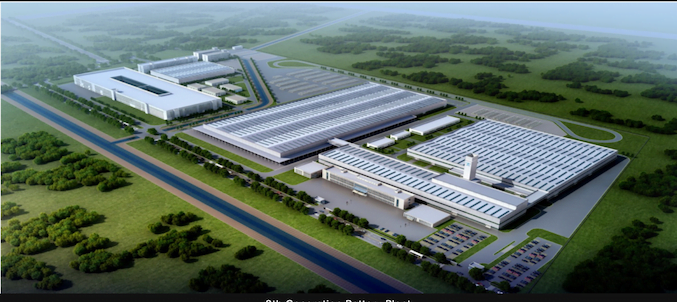
A US government pledge of US$2.9 billion support for the country’s battery manufacturing and recycling value chain is more like a band-aid than the “major surgery” required to fix the problem.
That’s the view of Adam Walters, a specialist renewable energy industry lawyer at Stoel Rives LLP. Energy-Storage.news reported earlier this week that the US Department of Energy (DOE) has unlocked the funding through the Infrastructure Investment and Jobs Act (IIJA), aka the Bipartisan Infrastructure Deal.
The DOE’s Office of Energy Efficiency and Renewable Energy will support battery materials refining and production facilities, as well as battery cell and pack manufacturing and recycling.
The administration has correctly identified the problems facing US industries, which currently import nearly all of their battery materials, components and often finished products too from abroad, and largely from China, Walters said.
However according to the lawyer, the funding, in the form of loans, doesn’t solve those problems by addressing their root causes, nor is it enough in dollar terms.
From starting out working with utility-scale solar companies in 2008, Walters has increasingly focused on the battery energy storage space. Last year he contributed to an article for our quarterly journal, PV Tech Power, on the inherent financial risks that battery storage companies face in their supply chains.
“While the administration has identified the right problems when it comes to the need to spur both battery supply chain manufacturing and raw materials mining in the US, the problem with US manufacturing has always been, and still is, high labour costs relative to Asia,” Walters said in comments sent to Energy-Storage.news yesterday.
“Under US$3 billion in short-term government loans is not going to change that either, when in industry terms, this is a small amount of money — basically enough to build two or three moderate sized manufacturing facilities.”
‘Proper solution remains to be realised’
In his PV Tech Power article, published last August, Walters had said that in the solar PV industry, Chinese government subsidies had blown European and American manufacturers “out of the water” from around 2011 onwards, with “very few survivors of that”.
The dynamics aren’t quite the same for batteries, he said, but US competitiveness versus the Chinese battery value chain is nonetheless facing an uphill battle.
“Unfair Chinese subsidies play a role, as they did with the solar PV industry a decade ago, but it isn’t to the same magnitude and tariffs aren’t the solution either; the proper solution remains to be realised,” he said yesterday.
In the shorter term, the COVID-19 pandemic is creating current high shipping costs and delays for internationally sourced products, which would make US-made products more competitive. However, Walters said, this is unlikely to have more than a couple more years’ impact.
“By the time new government-subsidised plants are up and running, global shipping costs will be back down to near pre-pandemic levels.”
In the rush to bring battery manufacturing, materials processing and recycling onshore, the lawyer also said there is a possibility that companies applying for loans might be affiliates of Chinese, South Korean and Japanese top tier players seeking to add manufacturing in the US, rather than US companies.
While in Europe, literally hundreds of gigawatt-hours of battery manufacturing capacity have been committed to — from a combination of domestically and overseas-headquartered companies — the majority of new large-scale manufacturing plants in the US are in construction by the likes of South Korea’s SK Innovation and LG Energy Solution, although US startup KORE Power is building a gigafactory in Buckeye, Arizona.