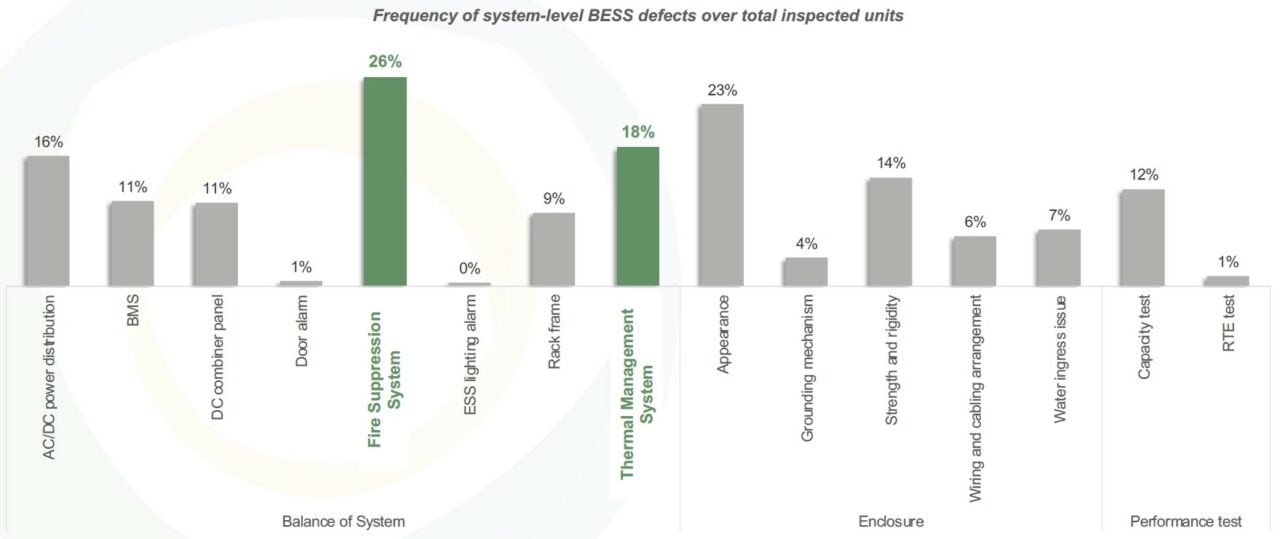
Of these issues identified, almost a third (26%) of BESS units inspected by the CEA had defects in the Fire Suppression System, while 18% of units had Thermal Management System defects, both of which are critical for functional safety, as defects in these systems can lead to increased risk of fire.
Some of the problems detected were a non-responding release actuator for the fire extinguisher agent, which, if malfunctioning, could potentially allow the fire to propagate further; non-responding smoke and temperature sensors, which wired incorrectly, could prevent the smoke sensor from detecting the presence of smoke within the system.
In the US, New York has been one of the leading states in its approach to safety issues regarding fires and earlier this month recommended changing the state fire code to better manage risks associated with battery storage systems installed in the state.
Moreover, an industry-led initiative from the American Clean Power Association (ACP) recently published a battery safety incident guide for first responders. Whereas in California, the state passed legislation last year that requires BESS owners to put in place safety and communications protocols with first responders and other key stakeholders.
Half of the issues came from system-level
These two issues – Fire Suppression System and Thermal Management System – were among the highest defects detected in the system integration of a BESS. Despite much of the industry’s attention being on cell selection, system-level should not be overlooked, as a potential source of problem, since these represent nearly half of (48%) the defects found by CEA.
A higher level of system-related issues is due to two reasons, the first is due to the BESS integration process being mostly manual and labour-intensive, while the second is problems originating from defects in upstream components might not have been caught in earlier quality checks.
Within that category, balance of system (58%) and enclosure (34%) had the majority of system-level findings. Although only 8% of the findings came from performance test, these had larger and more complex issues associated with them.
Recently, Energy-storage.news hosted a webinar with the CEA presenting some of the most common issues seen in the factory, their typical root causes and steps that can be taken in the manufacturing process to prevent these issues. During the webinar, George Touloupas, senior director of technology and quality, solar and storage at CEA, explained that the reason why the report focused on lithium-ion batteries was because: “Nobody is buying anything else than lithium-ion.”
One of the key takeaways from the report was that “quality assurance is the most efficient means to mitigate risks during mass productions,” added Touloupas.
Cell and module issues
Despite a higher automation process, cell issues represent 30% of the CEA’s issues found, with a third of the incidents occurring during electrode manufacturing, 38% during cell assembly and 30% during cell finishing.
The last category was for the module which represented 23% of the total findings, which is largely due to production lines being more manual. Half of the issues were related to interconnection wielding. This is due to the manual aspect of it and a lack of efficient quality control procedures.
For more details on issues related to each category, the report can be accessed here.