As BESS deployment surges internationally, driven by ambitious renewable energy targets and grid modernisation initiatives, the complex logistics of transporting these systems come into sharp focus.
BESS are commonly equipped with lithium iron phosphate (LFP) batteries. These batteries are temperature-sensitive and if mismanaged, abused or defective can cause high heat which can result in fire. For this reason, they are considered Class 9 Miscellaneous Hazards in US shipping.
This article delves into the evolving landscape of international BESS transportation, exploring key aspects like shipping routes, modes of transport, the impact of global disruptions, associated costs and future trends.
Leading shipping lines have recognised the growing importance of BESS transportation and offer dedicated services. These companies provide specialised solutions for BESS cargo, catering to factors such as temperature control, secure handling and efficient loading/unloading due to the often large size and heavy weight of BESS units.
Containerised versus modular: choosing the right shipping approach
The mode of BESS transport depends on the specific system design and capacity. Here’s a breakdown of the two main approaches:
Containerised transport
While containerised transport offers an efficient solution for shipping BESS units, factors beyond physical size must be considered for successful implementation.
First and foremost, the BESS system must comply with critical transportation regulations such as UN3534, ensuring the safe transport of lithium-ion batteries. Additionally, containerised transport necessitates standardised BESS unit designs.
Advantages
This standardisation ensures compatibility with ISO containers and facilitates efficient logistics throughout the transport journey. The BESS unit’s dimensions must seamlessly fit within standard ISO containers, typically 20ft or 40ft in length. This eliminates the need for custom packaging and simplifies loading and unloading processes at ports and destination sites. Standardised BESS units also facilitate easier handling throughout transportation. This reduces potential delays and complexities associated with non-standard designs.
Utilising readily available ISO containers offers significant cost benefits compared to custom packaging solutions, eliminating the need for custom-designed packaging for each BESS unit.
The robust construction of ISO containers also provides a secure and weatherproof environment for BESS units during transport.
Disadvantages
Standard ISO containers, even the larger 40ft models, have inherent size limitations. This restricts the total energy storage capacity that can be transported in a single container. For large-scale BESS projects requiring high capacity, containerised transport might not be feasible.
The requirement for standardised design might limit innovation in BESS technology. BESS system providers with cutting-edge designs that deviate from standard dimensions wouldn’t be suitable for containerised transport.
A further drawback of containerised transport is that it doesn’t offer much flexibility for project-specific customisations. This can be a disadvantage for situations requiring unique BESS configurations to meet specific site requirements.
A final major consideration is safety. Lithium-ion batteries, the core technology behind BESS units, pose potential safety risks during transport if not handled correctly. To address these concerns, the United Nations (UN) has established the UN Model Regulations for the transport of dangerous goods. Within these regulations, UN3536 specifically addresses lithium-ion battery installations in transport.
Compliance with UN3536 is a mandatory requirement for the safe and legal transport of containerised BESS units. By adhering to these regulations, BESS system providers, shipping companies, and port authorities can ensure the safe and efficient movement of these vital energy storage solutions.
However, meeting UN3536 regulations might necessitate using specialised packaging materials or incorporating additional safety features within the containerised BESS unit. These measures can add to the overall cost of transportation.
Modular transport
Advantages
Customised BESS systems or half-completed systems are typically transported in a modular fashion. This involves breaking down the system into its components, such as battery racks, enclosures, and power conversion systems (PCS). These components are then shipped separately and reassembled at the destination site.
Such an approach has a number of advantages, such as scalability. Modular transport truly shines in its ability to handle high-capacity BESS units. Unlike containerised transport with size limitations, modular transport allows for the transport of massive systems crucial for grid-scale energy storage projects. This flexibility accommodates the growing demand for the larger BESS project sizes that are increasingly common in maturing markets.
Modular transport also allows for customisation to cater to specific project needs.
Lastly, modular transport offers greater adaptability than containerised transport, which can be limited by port infrastructure or access roads. Individual components can be delivered by various methods, such as trucks, trains, or even barges, depending on the site accessibility and project requirements.
Disadvantages
As with containerised transport, modular transport has numerous downsides. For example, the separate transport of components necessitates additional documentation and permits compared to containerised transport, where a single container serves as the primary focus.
Modular transport doesn’t necessarily guarantee lower overall costs. Several factors can contribute to potentially higher expenses such as:
Unlike pre-assembled containerised units, modular systems require on-site assembly and commissioning. These processes involve labour costs, potentially specialised equipment and additional time compared to simply connecting a containerised unit. Successful reassembly of a modular BESS also requires skilled personnel with expertise in BESS technology and assembly procedures. The availability of such expertise at the destination site can be a crucial factor for project success.
Lastly, individual components during modular transport are more susceptible to weather elements compared to pre-assembled and enclosed containerised units. Implementing adequate weatherproofing measures during transport is essential to safeguard BESS components.
Understanding BESS transportation costs
The cost of transporting BESS units varies depending on several key factors. Larger and heavier BESS systems naturally incur higher transportation costs due to increased fuel consumption and potential limitations on containerised transport.
While specific costs can vary depending on project specifics, industry estimates suggest that transportation costs for BESS systems can range from 5-15% of the total project cost. Insurance adds an additional 1-2% to the overall cost.
Regulations for lithium-ion BESS transport
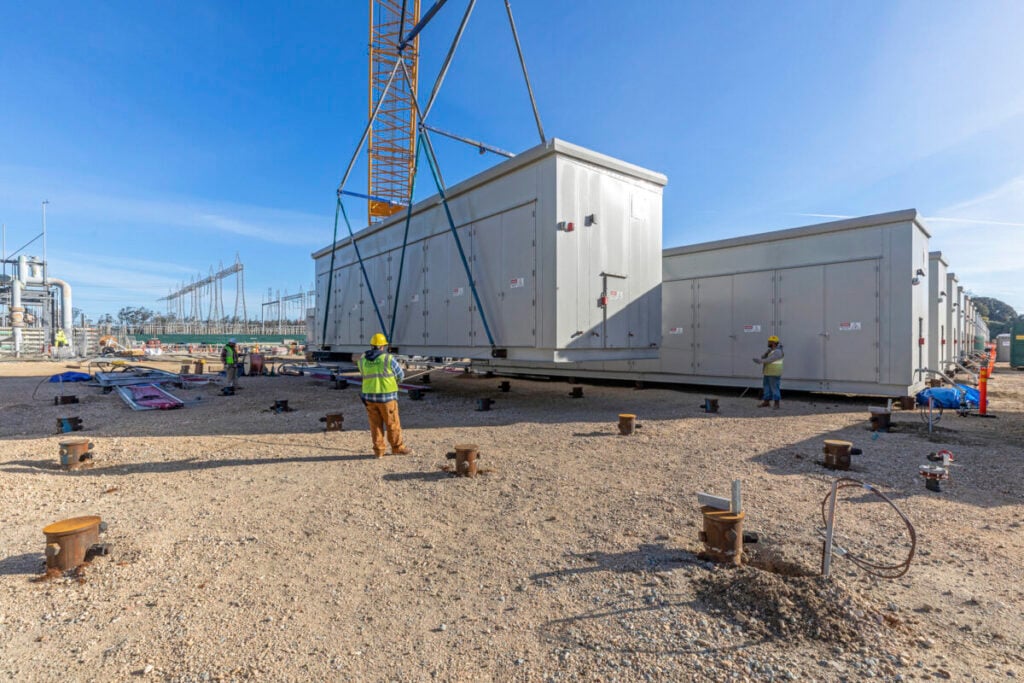
It is paramount to transport lithium-ion batteries safely. If not handled and transported correctly, lithium-ion batteries pose potential fire and explosion risks.
To address these concerns, in addition to the UN regulations, the International Maritime Organization (IMO) regulates the transport of dangerous goods, including lithium-ion batteries, under the International Maritime Dangerous Goods (IMDG) Code.
The chosen mode of BESS transport also impacts safety. Containerised transport generally offers a more controlled environment, with the entire BESS unit housed within a secure container. Modular transport requires careful handling and packaging of individual components to comply with IMDG Code regulations.
The future of BESS transportation
As countries like the US and Europe aim to reduce reliance on overseas manufacturing and strengthen domestic supply chains, BESS production facilities are expected to be built closer to these markets. This will significantly reduce transportation distances and associated costs.
Meanwhile, advancements in battery technology might lead to more compact and lighter BESS designs. This could facilitate easier and cheaper containerised transport for larger systems. For example, research into next-generation battery chemistries like lithium-sulfur holds promise for increased energy density, potentially reducing the size and weight of BESS units.
Nevertheless, the transportation of BESS systems plays a critical role in enabling the global energy transition. As BESS deployment continues to accelerate, a comprehensive understanding of the evolving landscape of international BESS shipping is essential. By optimising transportation strategies, minimising costs and prioritising safety, the industry can ensure the efficient and secure delivery of these vital energy storage solutions, paving the way for a more sustainable and reliable energy future.
This is an extract of a feature article that originally appeared in Vol.39 of PV Tech Power, Solar Media’s quarterly journal covering the solar and storage industries. Every edition includes ‘Storage & Smart Power’, a dedicated section contributed by the Energy-Storage.news team, and full access to upcoming issues as well as the 10-year back catalogue are included as part of a subscription to Energy-Storage.news Premium.
About the Author
Vienna Zhou, CEO of TROES Corp, is a seasoned expert with 17+ years in renewable energy, cleantech, and a background in Fortune 500 companies and government roles. With a mechanical engineering and MBA background, she founded TROES in 2018, an energy storage and microgrid solution company.