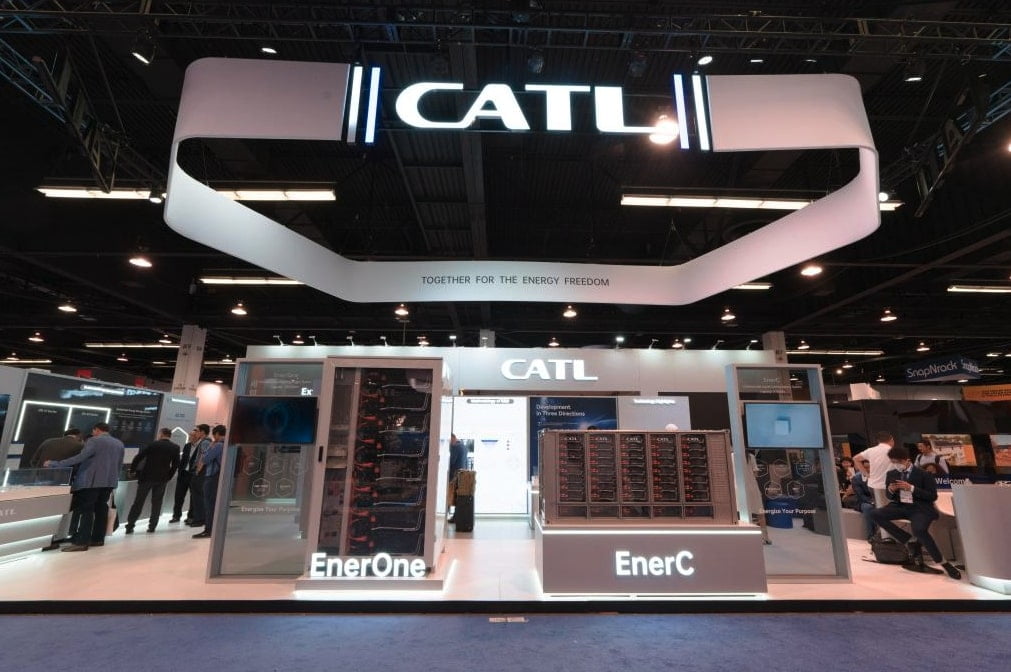
The risk of more restrictive trade policy in the future points to buying now, while technological advancements that promise energy density improvements favour delaying the procurement decision for a year or two.
First, the uncertainties
With virtually every utility-scale battery, reams of paperwork must be in order to demonstrate to US Customs and Border Protection officials that supply chains are free of forced labour.
Scrutiny has heightened in recent years following federal action that began in the solar PV sector aimed at preventing the import of solar modules that could contain components made by forced labour. A bill passed by Congress in late 2023 added new complexities.
A section of the National Defense Authorization Act that was approved on 22 December bars the Pentagon from buying batteries from Chinese suppliers alleged to have ties either to China’s military or the ruling communist party. The ban takes effect in October 2027 and targets CATL, BYD, Envision Energy Ltd., EVE Energy Co., Gotion High Tech Co. and Hithium Energy Storage Technology Co.
Although the enforcement date remains three years away, the congressional action had an immediate impact on the utility sector.
In early February, Duke Energy said it would decommission an 11MW/11 MWh lithium iron phosphate battery storage system at the Marine Corps base at Camp Lejeune, North Carolina. The system entered service in the spring of 2023 as part of a US$22 million energy services contract. It used a battery sourced from Chinese supplier CATL. Duke agreed to replace the CATL equipment with US-sourced battery technology.
That shutdown is the latest example of how trade policy between the two countries impacts US and Chinese businesses alike. The Camp Lejeune project’s high profile could result in ripple effects among other utility-scale project developers and their procurement decisions.
And the scrutiny over Chinese suppliers — which together control most of the global supply — comes at a time when battery design changes are driving efficiency gains that improve project economics by reducing balance-of-system costs.
From jelly roll to Z-stack
The improvements start with a shift from the standard “jelly roll” stack design to one that more closely resembles the letter Z. This shift allows for greater energy density within the same cell packaged into today’s standard 20-foot containers. That means a container using a Z-stack design can offer as much as 5.5-6MWh of capacity. Here’s how.
The jelly roll design layers the battery cell’s electrodes and separators. This cell is rolled into a cylinder and then inserted into a rectangular case. The roll does not fit cleanly into the rectangular can; instead, gaps are inherent in this approach and reduce the cell’s overall efficiency.
A Z-shaped design, by contrast, allows the electrodes and separators to be collapsed and folded to fit more neatly into the container. This design shift offers around a 10% volumetric energy density improvement using the same materials.
Liquid cooling
At the same time, manufacturers are moving away from air-cooled batteries to favour liquid cooling. That’s because cooling with air can result in uneven temperatures, which in turn can lead to accelerated cell degradation and safety issues. Liquid cooling reduces uneven temperature control and supports the move to larger Z-stack cell designs.
In practice, these improvements mean the same cell that earlier held a 280 Amp-hour (Ah) configuration can now hold a cell as large as 316Ah. This year and next will see a push by most manufacturers to install production lines to produce the more efficient Z-stack.
Battery maker BYD is taking a somewhat different approach to replacing jelly rolls. It introduced a blade-like design in which individual cells are placed in arrays when they are inserted into the battery pack. The company states this approach increases the battery pack’s space utilisation by more than 50% compared to earlier jelly roll designs.
Together, these developments leave procurement teams with a tough question: buy now and take delivery of what is a soon-to-be outmoded stack design or wait for a more energy dense Z-stack or blade model?
Buy or wait?
Given the uncertainty over potential congressional or Customs and Border Protection action, now may be the best time to import equipment from Chinese suppliers. Heightened scrutiny — akin to what solar PV procurement teams have experienced — raises the stakes and may lead to expedited buying decisions.
Prudent procurement teams will continue to demand robust traceability protocols and be ready to prove to border officials that components comply with forced labour federal requirements.
But buyers also shouldn’t lose sight of significant technological gains in the manufacturing pipeline — as Z-stack cell designs permeate the market, a patient, long-term view could pay dividends.
George Touloupas is senior director, technology and quality, for Clean Energy Associates. Jeff Zwijack is CEA’s senior manager of energy storage.