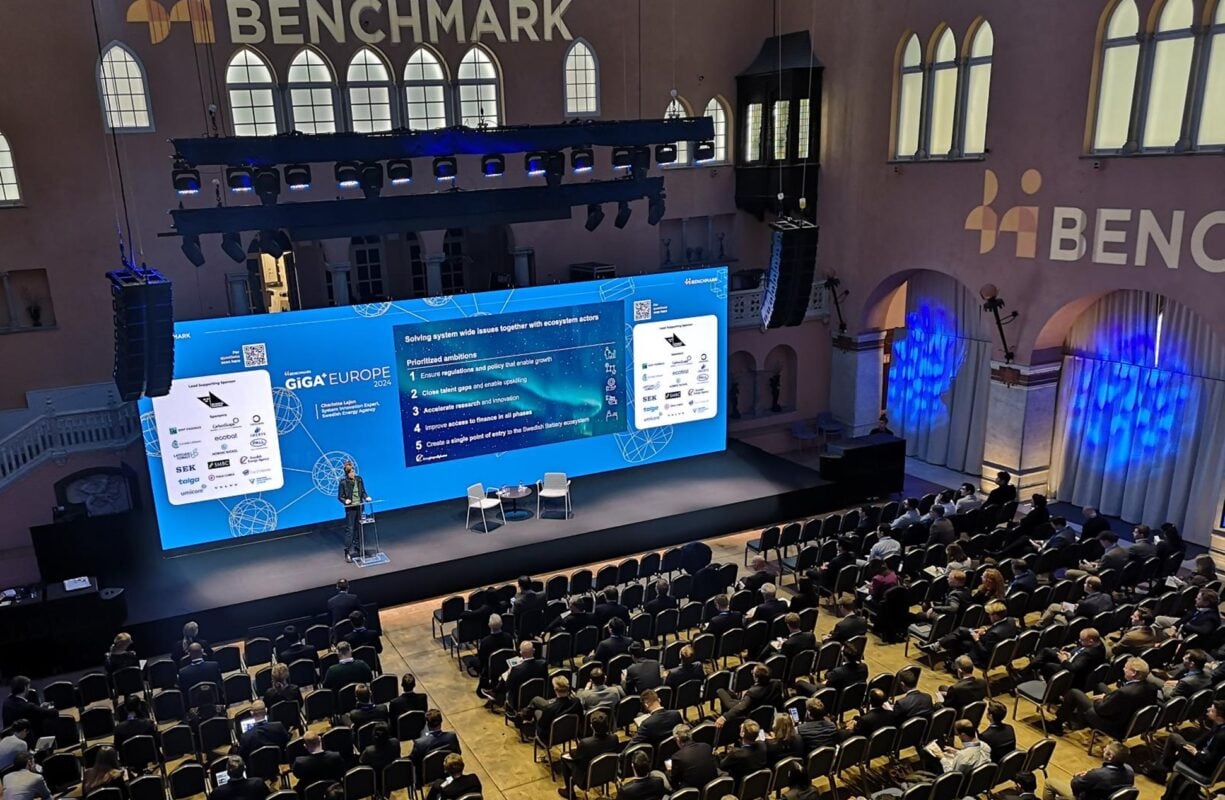
Research institute Fraunhofer ISE said last year that battery recycling capacity in Europe (including UK) by end-2023 would hit 160,000 tonnes, and reach 400,000 tonnes in 2025. It estimates that by 2035, there will be nearly 1,200,000 tonnes of battery or battery material needing an end-of-life solution on the continent.
Companies building the largest of these facilities include Ecobat, Altilium, Northvolt, Librec and EcoNili.
Most of this is for black mass production – collecting, testing and then shredding battery material – but just under half of recycling facilities will have the capability to then refine black mass and recover the critical materials, like lithium, cobalt and nickel, Fraunhofer ISE said.
If they were all whole lithium-ion batteries, 400,000 tonnes of battery material would cover around 1-3GWh based on the current average weight of a battery, though the majority of the volumes recycled will be battery scrap from battery manufacturing (around 65% according to Ecobat’s Tom Schaefer). As much as 10-30% of the raw material inputs into lithium-ion battery production come out as scrap.
End-of-life requirement for EV and ESS driving investment in recycling
The primary driver of these investments in recycling is EU rules requiring those selling batteries to have an end-of-life solution in place from the very beginning. This applies to all segments, including electric vehicles (EVs), energy storage systems (ESS) and consumer electronics.
This is why Northvolt, Europe’s biggest home-grown gigafactory company by planned capacity, has recycling capabilities at its flagship Ett plant in Northern Sweden as well as through a JV entity, Hydrovolt, in Norway.
The end of February also saw another Nordic battery gigafactory firm Morrow Batteries sign an agreement with recycling company Stena, under which Stena will process battery scrap from Morrow’s first gigafactory. Morrow is one of the few primarily targeting the ESS market, and we interviewed both companies at Giga Europe.
Stena’s Per Hellberg told Energy-Storage.news that companies in the ESS space are signing deals that cover the entirety of a project’s lifetime, with agreements to recycle some smaller volumes periodically as the project degrades before the entire system needs to be replaced at the end of its life.
Full replacement or recycling of a projects’ BESS capacity is being seen at select sites recently, including a 4.6MWh project in Hawaii and a 44MWh project in Illinois, US last year, and more will be coming as projects age.
Onshoring supply chain
Other delegates Energy-Storage.news spoke to agreed that recycling is also seen as a core part of increasing the amount of locally available critical materials the continent’s gigafactory projects will need to reduce dependency on China. Mining is obviously the primary route to this, but the sector faces huge challenges in having public acceptance for projects.
The focus on recycling may come at the expense of second life energy storage, which involves redeploying use EV batteries into stationary ESS. Stena sold its second life energy storage arm BatteryLoop in September, to a new, EU-backed company Repono. (Energy-Storage.news will write a separate article on the second life sector more broadly in the coming weeks.)
NMC (nickel-manganese-cobalt) chemistry is currently the main focus for recycling projects in Europe that have a refining capability, because of the much higher value of the metals that come out of it.
“There is very little LFP (lithium iron phosphate) refining capability being built in Europe,” Hellberg said. That also reflects NMC being the focus of most gigafactory production, mostly because of focus on EVs which much more commonly use that chemistry over LFP. Within recycling broadly, there is more focus on setting up black mass recycling than refining because of its comparatively lower capex requirements.
Both Stena and Ecobat take all types of batteries for their black mass produced, but material from LFP cells would then need to be shipped out of Europe for further processing and refinement for the foreseeable future (to a greater extent than for NMC).
Energy-Storage.news was told that China is the only country putting substantial investment into end-to-end LFP recycling capabilities because it sees controlling lithium as key to continuing to dominate the global battery market.